本节书摘来自华章出版社《制造业中的机器人、自动化和系统集成》一书中的第3章,第3.1节,作者[英] 麦克·威尔逊(Mike Wilson),更多章节内容可以访问云栖社区“华章计算机”公众号查看。
3.3 工艺设备
自动化系统可以分为两类:用来装配、机床上下料或常见的材料搬运操作的自动化系统;实现某种加工工艺的自动化系统。前一类往往使用安装于机器人上的抓手,而后一类需要一些工艺设备来控制和实施该项工艺。这些工艺包括:
●焊接
●喷涂
●粘接和密封
●切削和49材料去除
这些工艺大部分可以手工完成,并且最初的机器人应用基本上就是把手动设备安装在机器人手臂上来重复手工操作。然而,随着技术的进步,工艺设备得到了长足的发展,已经可以适用于自动化应用和技术,有些工艺设备更适用于自动化应用。这已经使得工艺系统能够与机器人的机械系统和控制系统紧密集成,为我们提供更有效、稳定和可靠的解决方案。本书并非想要囊括所有的工艺过程,而是讨论有关机器人应用于这些工艺过程中的关键问题。
3.3.1焊接
最典型的焊接工艺是点焊和弧焊。弧焊又涉及很多工艺过程,比如金属极惰性气体保护焊(MIG)和钨极惰性气体保护焊(TIG)。
点焊
点焊是用力使两块板贴合,在接触点通以电流并产生金属熔融物,将两块金属薄板焊接到一起。这一方法广泛应用于车身制造。点焊钳包含两个臂,每个臂有一个触头。两个臂通常采用气动,当触点与金属板接触时,提供压力使两块金属板靠近,消除两者之间的缝隙。变压器输出电流,电流流过焊钳臂和触点组成的回路,在这一过程中会在接触点产生热量并使金属融化。控制这一过程的关键参数是提供的电流大小以及接通电流的时间长短。
焊钳臂的大小及设计由被焊接的工件决定。触头需要放置在被焊工件边缘的两侧,因此焊钳常常很大、很笨拙。这就很难通过人工操作将焊钳定位到正确位置。然而,机器人可以应付笨重的焊钳,并能够快速且准确地定位。于是,点焊成为并且依然是主要的机器人应用领域。
随着机器人负载能力的提升,使得将变压器集成到焊钳中成为可能,这也减小了连接焊钳电缆50的尺寸。焊接控制器或焊接定时器如今也被集成到机器人控制器中,为用户提供一个完整的机器人点焊包。关闭焊钳臂的驱动方式也已得到了发展,并且如今我们可以把伺服电机集成到焊枪内,利用伺服电机驱动焊钳臂的开闭。这个动作由机器人程序控制,就像机器人控制关节轴运动一样。焊钳的控制也因此变得更加紧凑,不仅可以实现气动的开关动作,还可以让焊钳臂移动到特定的位置。焊钳打开的角度可以最小化,焊钳可以在机器人到达焊接位置之前关闭,这就可以减少焊接过程所需的时间。
点焊机器人的另一个重要因素是管线包。它是将电、气、液等服务条件由机器人底座传送到焊钳的线束。管线包是承受最多磨损的工件,因为它与机器人焊钳的转动相关联。经常是管线包造成机器故障,而不是机器人本身或者焊钳。点焊机器人已经发展到尽可能将管线包集成到机器人手臂中,包括将线束穿过一些轴的中心。还有一些专门设计的管线包(如图3-2所示)来适应点焊机器人的这些特性,其总体目标是减少线缆的磨损并提高整个点焊系统的可靠性。定期更换电极帽也是很重要的,因为电极帽会随时间变形。自动电极帽修整器能够提供全自动维护功能,因而最小化维护操作。
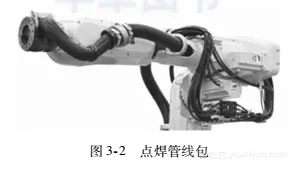
弧焊
弧焊利用电弧产生的热量使两块金属融在一起。不像点焊需要电极帽在工件两侧接触,弧焊只需要接触工件的一侧。MIG焊的电弧由金属丝产生,金属丝也会熔化在焊缝,填充焊缝。TIG焊并不51提供额外的金属,除非使用外加的填充金属丝,因此焊缝完全由焊缝处的金属熔化形成。由惰性气体在电弧处形成的保护层来避免金属氧化。MIG焊广泛应用于汽车部件、越野车辆以及常规金属制造中。而TIG焊更适用于高精度加工,尤其是薄板工件。大多数的机器人焊接使用MIG焊。最重要的参数是金属丝的进给速度、电压、通过的电流以及焊枪头与焊缝隙之间的距离,还有焊枪沿焊缝的运动速度等。
MIG焊接机器人在其手腕的末端安装焊枪。在大多数的应用中,焊枪都是水冷的。焊丝喂给焊枪,通常由安装在机器人小臂的送丝机驱动,并将焊丝送给焊枪。焊丝盘一般安装在机器人基座上,或者置于机器人焊接单元外。管线包也将惰性气体和水输送给焊枪。管线包的设计和安装对于整个焊接系统的可靠性以及稳定地将金属丝输送给焊枪处十分重要。与点焊机器人类似,机器人手臂和管线包已经发展到使电缆的磨损最小化,包括电缆直接通过机器人手腕到达焊枪。
焊接过程通过焊接电源控制,电源往往靠近机器人放置。焊接过程由焊接电源控制,完全集成到机器人控制器中,以便实现最佳焊接参数的选择,从而适应各种焊缝的类型、焊丝伸出的长度以及移动速度。这些通常编程到工艺表中,以便机器人程序在恰当的地方调用正确的参数。对于较大的焊缝,在焊接过程中,按照标准的预先设计的指令,机器人路径可编程为往复摆动,摆动焊枪通过缝隙,这样有助于完成焊接过程。
工件拼装和定位的重复性是焊接成功的关键。对于较大的工件,比如越野车辆、桥梁以及其他重型装备,这些是较难实现的。如今的技术已经发展到了可以生产适应工件变化的机器人。最简单的是触觉,机器人可以使用焊枪的尖端接触焊缝的特征。当焊枪接触后便感知到位置,因此就可以判断焊缝的位置。第二个功能是通过电弧追踪焊缝。当机器人摆动通过焊缝时52,焊接电流会随着焊丝伸出的长度而变化。通过监测电流,焊枪的位置便保持在焊缝中心上。这种功能的应用被特定的焊缝类型与金属厚度所限制,焊接过程中需要摆动就是其限制因素之一。因此,利用视觉系统实现焊缝追踪的功能就被开发出来。然而,这些系统极大地增加了机器人焊接系统的成本和复杂度。
在机器人焊接应用中,往往需要翻转工件,以便机器人能够达到所有焊接位置。比如,汽车的排气系统由多根管子焊接而成。这就需要管道与消音器之间的焊缝实现360°焊接。为了达到这个要求,就需要旋转焊接工件,以便有利于机器人焊接。这可以由一个单轴伺服驱动变位机来完成。为了达到最好的焊接效果,需要6轴机器人的动作与伺服变位机很好地协调。
变位机的形式多种多样,最简单的变位机带有伺服驱动的头部和尾座(如图3-3所示)。这些可以扩展为两工位变位机,并带有安装在转盘上的头部和尾座(如图3-4所示)。这可以让操作者在机器人工作的同时,在另一边卸载和重新装载工件。并且,当需要在两个方向定位工件来达到最佳焊接位置时,可以使用两轴变位机(如图3-5所示)。这种两轴变位机也可以扩展成为两工位变位机。对于长度较大的工件,还需要伺服驱动的机器人导轨。53机器人也可以倒挂安装在头顶位置,在某些情况下这种安装方式可以更好地到达焊缝位置。有很多不同的变位机与机器人的组合可供选择,为典型的机器人应用做周边设备选型将在5.2.1节讨论。

机器人焊接包中的最后一个组件是焊枪维护系统(如图3-6所示)。在焊接过程中,焊枪会被焊渣堵塞,这就需要定期清理来保持焊接过程的可靠性和焊接质量。该任务由自动清理器完成,它包括清理焊枪内部的镂铣装置和喷油装置(减少焊渣黏着)。焊枪维护系统还包括一些传感器,它用来检查焊枪位置以及修正偏差。这些偏差可能来自碰撞、焊丝粘贴问题(在焊接结束后金属丝依然黏着在熔池中)或者人工维护。
3.3.2喷涂
喷涂往往被认为不同于其他的大多数自动化工艺。这在某种程度上是有历史原因的,不仅自动喷涂方法的开发者与实现其他自动化应用的人来自不同的领域,并且工艺要求以及所用语言与其他应用也不相同。
有许多不同形式的自动喷涂设备,比如往复式喷涂机和静电杯喷涂系统,但是在本书中,我们将主要讨论机器人喷涂系统。机器人喷涂系统被应用于许多产品中,从车身、汽车部件到复杂的飞行器。机器人喷涂的一个关键特征就是防爆,因为它们一般应用于富含溶剂的环境中。为了实现防爆,需要不间断地用清洁空气净化机器人手臂,并且控制器也在标准版本的基础上做了改进。
由机器人系统处理的喷涂工艺有许多种类,包括溶剂喷涂、水基喷涂以及二元喷涂和粉末喷涂。每一种都需要不同的输送和应用设备。机器人可以使用标准空气雾化喷枪、静电喷枪和静电杯。喷射装置的选择一般由工艺和客户要求决定。颜色变化等问题十分重要,机器人的机械臂中可以包含大量的颜色变化值,以便为喷射枪提供颜色变化,使转换时间达到最小,并减少涂料浪费。机器人也可以包含全部的工艺控制,涂料流量、雾化空气,以及其他工艺参数都可在机器人程序中选择和控制。这就可以完全控制特定工件以及每种颜色的工艺过程。
机器人可以工作在连续移动流水线和间歇流水线中。56可以利用输送机全程跟踪技术,来确保机器人正确跟踪移动的工件。机器人还可以安装在轨道上来跟踪整个喷涂车间的工件。对于汽车喷涂应用,门、发动机罩和行李箱等,开启装置的应用使机器人可以实现内部喷涂。
喷涂是一项较为复杂的机器人应用,需要对工艺有很好的理解来确保机器人功能正确,实现所需要的结果。
3.3.3粘接和密封
粘接和密封应用一般是通过挤压或喷射装置。挤压需要接触或密切接近被加工材料的表面。喷射则与工件之间保持一定距离,因此允许路径准确度有较大的误差。
粘接和密封使用的材料可能是一元或二元。一元材料可能需要加热,这种情况下需要一个热炉或其他类似的加热装置。二元材料在混合时就开始处理,因此,从系统中喷出混合成分的方法显得十分重要。
典型系统一般包括一个(一元)或两个(二元)泵来提供材料,可能还有流量控制。温度条件也需要考虑,以便确保最佳的材料性能。如果有利于整个系统的运行,那么这些装置都可以集成到机器人系统中,特别是流量控制。
3.3.4切削和材料去除
有许多切削和材料去除技术,其中大多数都可以应用到机器人中。切削技术包括锯削、铣削和水切割。圆锯已经应用到机器人中,去除铝合金压铸件的浇铸口。铣削可以使用气动或电动工具。电动工具通常较重,这就需要机器人有更高的有效负载。最重要的是为材料切削选择正确的工具,然后以此开发机器人切削系统。另一个十分重要需要考虑的是切削工艺中产生的粉尘57,主要是为了操作人员的安全,在某些情况下机器人也需要额外的防护。废弃材料的清理也非常重要,以便确保积累的废弃物没有妨碍机器人系统的运行。
水切割是很好的机器人应用。水射流可以完成非常干净的切削,尤其是对于铸造或成型的塑料件。机器人可以提供三维切削方案,这在其他设备上是不可能完成的。由于在水切割车间内有高强度水流,所以为了在这种环境中应用机器人,需要对机器人进行额外的防护。另外,切削过程中水的供给也需仔细考虑。由于需要高压,所以给切割头供水的管子不能是软管。如果机器人安装了切割头,一般将一圈不锈钢管子从机器人的大臂处绕到切割头上。这将使机器人能够在3个方向旋转切割头,而管子是否缠绕起来由转动方向来决定。
其他材料去除应用包括抛光和去毛刺。这些工艺都要求特定标准的表面光洁度,因此,工艺过程和工艺设备十分重要。如前文所述,使用正确的工具十分重要。去毛刺经常由安装在机器人末端的工具完成,可以是气动或电动工具。抛光则经常通过将工件压到一系列砂带上来完成,每条砂带都有不同目数。这些砂带经常安装在外置的抛光机上,抛光机驱动砂带运动,同时保持并提供合适的张紧力。为了提供最终光洁度,布轮抛光是必不可少的,它要求机器人抓住工件并承担抛光布轮施加的抛光力。
这些应用要求工件与工具之间接触。因此,某种形式的顺应性对于适应工件或工件位置的变动是必不可少的。这可以通过使用气动技术来实现,为工具提供顺应性,或者利用机器人内置的软件。然而,如果系统中引入了顺应性,加工效果很可能发生变化,这是由作用力或者工件上的切削深度不完全一致造成的。如果这种加工效果的变化是不能接受的,那么就需要在机器人内包括力控制。可以在工具和机器人腕部之间安装力传感器来完成力控制。这样就可以把施加到机器人上的作用力反馈回去,并且可以用来控制机器人运动路径,从而实现想要的结果。